The April 2012 item by Jan Suszkiw of the US Dept. of Agriculture (on the Western Farm Press website) seemed strangely familiar as it focused on research into flame-retardant cotton. From the Suszkiw article,
In one ongoing project, the researchers have teamed with Texas A&M University scientists to evaluate a first-of-its-kind, environmentally friendly flame-retardant for cotton apparel and durable goods. Halogenated flame retardants have been among the most widely used chemical treatments, but there’s been a push to find alternatives that are more benign and that won’t cause treated fabric to stiffen, according to Condon [Brian Condon, Agricultural Research Service [ARS]).
I mentioned the research work in the context of a 2011 meeting of the American Chemical Society in my Sept. 6, 2011 posting (scroll down about 3/4 of the way) except the focus was on the Texas A&M University in College Station research team who had yet to collaborate with Condon’s team at the ARS,
In responding to the need for more environmentally friendly flame retardants, Grunlan’s [Jaime C. Grunlan] team turned to a technology termed “intumescence,” long used to fireproof exposed interior steel beams in buildings. At the first lick of a flame, an intumescent coating swells up and expands like beer foam, forming tiny bubbles in a protective barrier that insulates and shields the material below. The researchers are at Texas A&M University in College Station. …
Since the meeting last fall, the two teams (US ARS [Condon] and Texas A&M [Grunlan]) have collaborated to make cotton more flame retardant according to the April 2012 news article (Cotton Gets Nanotech and Biotech Treatment in New Orleans) on the US Dept. of Agriculture, Agricultural Research Service website (Note: I have removed a link),
Condon and CCUR (Cotton Chemistry and Utilization Research Unit) chemist SeChin Chang are collaborating with Texas A&M University (TAMU) scientists to evaluate a first-of-its-kind, environmentally friendly flame retardant for cotton apparel and durable goods.
Halogenated flame retardants have been among the most widely used chemical treatments for cotton. But there’s been a push to find alternatives that are not only more benign, but that also avoid imparting the same stiffness to fabric characteristic of some chemical treatments. For these and other reasons, “the textiles industry would like to move away from using halogenated flame retardants,” says Condon.
Made of water-soluble polymers, nanoscale clay particles, and other “green” ingredients, the ARS-TAMU flame retardant is applied as a nanocoating that reacts to open flame by rapidly forming a swollen, charred surface layer. This process, known as “intumescence,” stops the flame from reaching underlying or adjacent fibers.
A team led by Jaime Grunlan at TAMU’s Department of Mechanical Engineering, in College Station, Texas, originally developed the intumescent nanocoating using a layer-by-layer assembly. In this procedure, alternating layers of positively and negatively charged ingredients, including clay particles 50-100 nanometers wide, are deposited onto the surface of a desired material. The result is a striated nanocoating that, when viewed under a scanning electron or other high-powered microscope, resembles the stacked layers of a brick wall.
Condon’s interest was piqued after listening to Grunlan discuss his team’s research at a recent American Chemical Society meeting, and he approached the TAMU professor about potential benefits to cotton. That conversation, in turn, led to a cooperative research project enabling Condon and Chang to evaluate the nanocoating at CCUR.
Treating cotton for flame resistance isn’t a recent concept, adds Condon, whose lab is part of the ARS Southern Regional Research Center in New Orleans. In fact, some of the most successful early treatments were born of research conducted by Benerito [Ruth Benerito] and colleagues there several decades ago. (See “Cross-Linking Cotton,” Agricultural Research, February 2009, pp. 10-11.) Condon coauthored a 2011 ACS Nano paper on the potential of intumescent coatings together with Chang, Grunlan and his TAMU team, and Alexander Morgan of the University of Dayton Research Institute in Ohio.
Early trials of the nanocoating using standard flame-resistance tests are promising. In one case, 95 percent of treated cotton fabric remained intact after exposure to flame, whereas the untreated fabric used for comparison was completely destroyed
“What we’re investigating now is how well it will perform after repeated launderings of treated fabric,” says Condon. “After all, the coating contains clay, and that’s something detergents are made to remove.”
Even if the coating does eventually wash out and the treated fabric loses its flame resistance, the nanotech approach could still be used to protect textiles and durable goods that aren’t frequently washed, such as upholstery, mattress pads, box spring covers, automotive interiors, and firefighter coats.
This is one of the images that accompany the article,
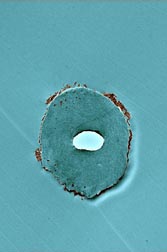
Cross-section of a cotton fiber with clay nanoparticles attached. (from: http://www.ars.usda.gov/is/AR/archive/apr12/cotton0412.htm)
If you are interested in the work being done by the US Dept. of Agriculture’s Agricultural Research Service on cotton, there’s a lot more than I managed to excerpt.